Equipment Inspections
If you or your business regularly uses lifting equipment, it is your responsibility to manage and control the risk involved, and ensure that your equipment is fit for purpose. Here at Lifting Gear Direct, we can offer official LEEA (Lifting Equipment Engineers Association) accredited lifting equipment inspections, to ensure that your lifting gear meets health and safety standards.
LOLER Regulations
Under the Lifting Operations and Lifting Equipment Regulations (LOLER), it is recommended that your lifting gear should be inspected at least every 12 months, or more often dependent on the frequency of use. Operating faulty lifting equipment can be extremely dangerous, so regular lifting equipment inspections are essential to ensure the safety of you, your equipment and your workforce.Approved LOLER lifting equipment inspections
The LOLER regulations state that you must ensure that all lifting equipment is safe to use, is operated safely and that is continues to stay safe for use. Our team can assess your equipment to ensure that it meets these criteria through thorough inspection and testing. If we do find any issues with your equipment, we should be able to rectify these for you, performing any repairs or replacing any parts required. Once your lifting equipment inspection passes, we’ll issue you with an official certificate, proving that your equipment is safe to use. For your convenience, our friendly, expert lifting gear inspectors are happy to visit your site in order to inspect your equipment, or, alternatively, you can bring your equipment to us. If you’d like to book a lifting equipment inspection with Lifting Gear Direct, get in touch today. Call 01384 76961 or contact us online.Our Qualified Inspection engineers can carry out inspections and repairs on all types of Lifting Equipment
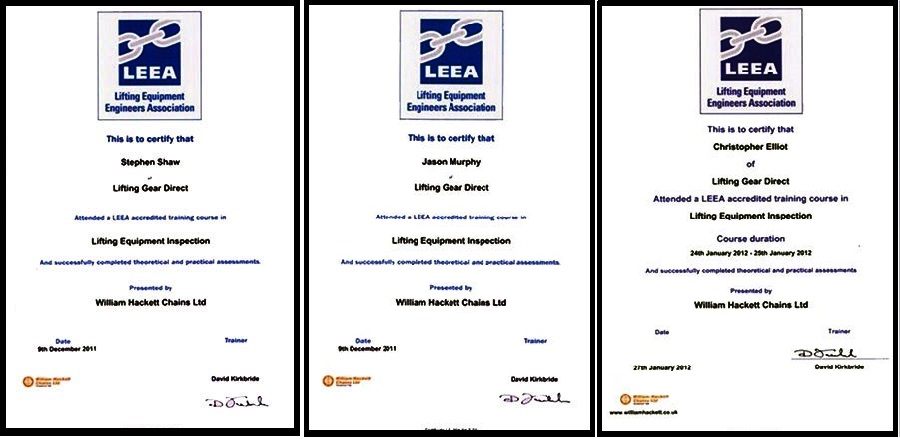
Here are some examples of damage found during routine chain inspections; bent, cracked or distorted chain should not be used until repaired or replaced.

Lifting equipment needs be checked on a regular basis
It is easy to understand the strenuous work which all types of lifting equipment go through on a daily basis, and because of this, wear and tear and other problems are inevitable. It is for this reason that all your lifting equipment should be checked on a regular basis, before each use is the best policy to adopt, that way any potential problems can be identified and rectified before the lift takes place and therefore reduce the risk of equipment failure and the consequent injuries which may occur.In 1998 The Lifting Operations and Lifting Equipment Regulations (commonly referred to as LOLER) became a legal requirement, with its aim to minimise any potential health and safety risks that may occur when using any type of lifting equipment in the workplace.With regards to LOLER, the regulations refer to three criteria, 1: the lifting equipment, for example; a hoist or gantry; 2: Lifting accessories, for example; shackles, slings and eye bolts; 3: The lifting operation, which refers to the actual lifting, lowering and movement of the load.Three categories within these regulations state you must ensure “1: the lifting equipment is safe to use; 2: it is used in the correct and safe manner; 3: it continually remains safe to use “(i.e. inspect, maintain, repair).Adherence to the regulations
To ensure all lifting equipment adheres to the last category, lifting equipment must be inspected at yearly intervals; lifting accessories and equipment which is used to lift people must be inspected at 6 monthly intervals. In addition directions for the safe use of the equipment must be issued and the employer must ensure they are followed and the equipment is used correctly. All records of inspections and testing must be kept by the employer.LOLER regulations are enforced by Health & Safety inspectors; where serious hazards are identified, and the requirements are not new ones, inspectors will be in a position to take firm enforcement action where required.Without these inspections lifting equipment may not only fail to function properly, but they also can cause serious safety issues for those using them and those around them when they are being used. Inspections should be used as Planned Preventative Maintenance (PPM) and a reputable lifting equipment company should be able to schedule your inspections on a regular, yearly basis, or sooner if necessary. By setting up a regular inspection and maintenance program with us we will do all the hard work and contact you a few weeks prior to your inspection due date to book you in, we will then have our qualified engineers carry out the necessary inspection and servicing procedures relevant to your equipment, any problems which are identified, can often be rectified swiftly, if not, a replacement product can be purchased directly.Please take note that the above content is only a very brief insight into lifting equipment inspections, for further and more complete information please refer to LOLER and/or health and safety in the workplace Click HERE. You can also visit the LEEA (Lifting Equipment Engineers Association.
Get in touch today
To discuss above or enquire about our lifting equipment inspections, call our team on 01384 76961. We also offer a range of other services such as in-house and on-site load testing, breakdowns and installation services.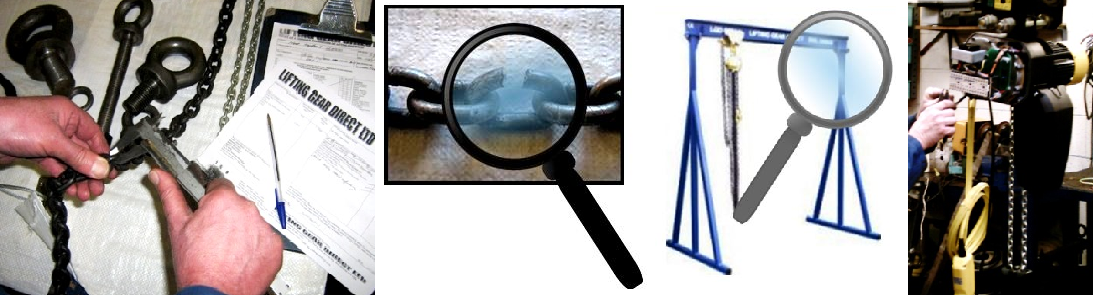